Trunnion Tables, T5Cs, and TRTs are usually mounted in the centre (or slightly off-centre) of the mill table. If you are using probing on the mill, be aware of the interference with larger tools, especially during tool changes.
NOTE: Trunnion units present interference issues with the swing of the unit relative to the machine column and spindle head.
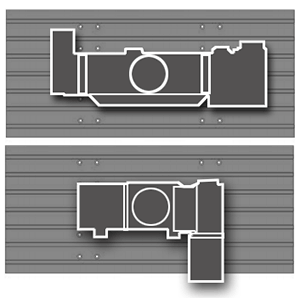
Image shown for mounting example purposes only. Your actual rotary and mill appearance may differ.